About GreenLINE Floor
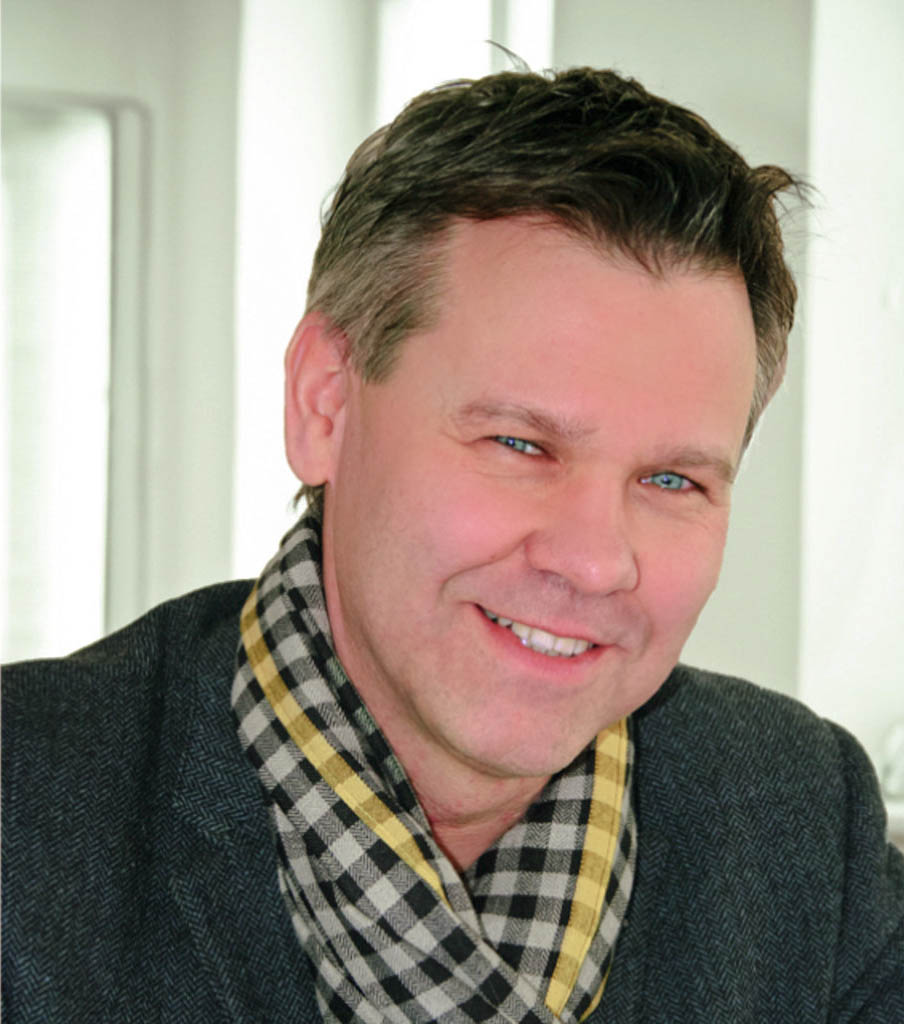
Intensive manufacturing processes and modernization in production and storage technology are unstoppable and demand the utmost from industrial floors every day. The permanent strain on floors, whether in the food industry, in machine and tool halls or in underground car parks, leaves its mark. The time of repair measures are approaching and the client and architect are making a decision as to which industrial flooring solution should be installed. More and more decision makers are choosing industrial floors with ecological components. Why this is so, the Greenline floor expert answers:
What makes Greenline Floor different from conventional industrial floors?
Oliver Jost:
The durability and the cost factor. But also the ecological aspect. Taking all these factors into account, the client inevitably comes to the conclusion: the floor must be made of concrete! Concrete floors are very stable. However, without appropriate finishing, they too are subject to wear and tear. Erosion due to abrasive stress, abrasive media such as quartz sand and stress from aggressive media such as alkalis, acids and oils can cause changes that require renovation. In the case of industrial floors made of synthetic resins, it can happen that the protective coatings have to be extensively reconditioned after eight to ten years because they are scratched or damaged. In some cases they are undermined by water, so that they dissolve over large areas. Due to the removal and clearing work and the curing times of the synthetic resins, the renovation of the coatings leads to a shutdown of operations that can last up to seven days.
The upside?
Oliver Jost:
It’s completely different with this procedure. There are many advantages. The method developed by Greenline Floor Systems in a development process lasting many years and now offered under the Greenline Floor label is unique. First, the surface is sanded. Already, during this process an impregnation is applied, in order to achieve a certain penetration depth. This changes the matrix of the concrete. After polishing and finishing, the floor is impregnated again and receives its oil, acid/alkali resistance and waterproofing. The special properties of the concrete floor are achieved without the need for any burdening epoxy resins or similar. All impregnations are mineral-based. This is why Greenline Floor Systems calls its development an ecological industrial floor. A significant advantage of this process is that the work steps can be carried out during ongoing operations. The operations are absolutely dust free and the surface may be walked on shortly after treatment. Greenline Floors can even be installed on construction sites, even in cold halls. While coatings often require a temperature of 12°C to cure – which can lead to long delays on construction sites, especially in winter. Greenline Floor eliminates this limitation. As soon as a hall has a temperature of 5°C, work can begin. There is no need to interrupt operations. This is not the only economic advantage of the process. The purchase costs are up to 20% lower than for a coated industrial floor. The follow-up costs, which must be included for maintenance and cleaning, are reduced to a minimum.
And the safety aspects?
They have been maximized: The floors have been classified as accident-preventing due to their anti-slip properties and are also non-combustible. With the appropriate care with Greenline Polish Pads, they have an almost unlimited lifetime without changing their appearance. Depending on the depth of sanding, the floor will have a terrazzo appearance. This and the technical properties must be protected. This is an argument that especially companies whose floors are exposed to increased stress cannot ignore. The effectiveness of the impregnations is constantly checked by our own tests. Of course, the opinion of customers who have already used the Greenline Floor process plays a role.
At what time window does your work start?
Oliver Jost:
Work can actually begin at any time. In new buildings, the first impregnations are applied directly to the fresh concrete to give the concrete better properties right from the start. These are fewer cracks, increased compressive strength and faster hardening of the concrete. With older material, any time is possible. The procedure according to GLF Technology® is practically unlimited, and can be applied to concrete at any time. After a detailed consultation, the best point in time is determined, so that for renovations in industrial halls and for new buildings in industry, as well as for objects with increased visual requirements, the point in time is chosen without interfering with the other processes.
What about the ongoing production or logistics processes?
Oliver Jost:
As mentioned earlier, many businesses can operate concurrently with production because GLF Technology® ensures dust-free processing of floors. There are no drying and curing times as with other systems.
And the question of costs?
Oliver Jost:
The costs are 20-30 % lower; and that is calculated on the basis of the total renovation measures. If the service life of the floor is also taken into account, the question of costs no longer arises.
BMF Bodentechnik GmbH (www.bmf-bodentechnik.de) renovates and designs industrial floors specially adapted to the wishes of the customer.
The proprietary development GreenLINE Floor® is an ecological industrial floor based on concrete floors. www.greenlinefloor.de