Industrial Floors
Concrete floors are very stable. However, without appropriate finishing, they are subject to wear.
Erosion due to abrasive stress, with abrasive media such as quartz sands and stress from aggressive media such as alkalis, acids and oils can cause changes that require renovation.
In the case of industrial floors made of synthetic resins, the protective coatings have to be laboriously reconditioned after eight to ten years because they are scratched or damaged. In some cases they are penetrated by water, so that they dissolve over large areas. Due to the removal and clearing work and the curing times of the synthetic resins, the renovation of the coatings leads to a shutdown of operations that can last up to seven days.
After polishing and finishing, the floor is impregnated again and receives its oil resistance, acid and alkali resistance and waterproofing. The special properties of the concrete floor are achieved without the use of any epoxy resins. All impregnations are mineral based. Therefore, GreenLINE Floor Systems calls its own development an ecological industrial floor.
5 Good Reasons for GreenLine Floor
1. Long service life with minimum maintenance
2. Significantly improved cleanability due to a smooth surface
3. Cost savings of up to 20 percent compared to other floor systems
4. Low noise forklift traffic, no tyre tracks and less vibration
5. Anti-slip properties
Procedure
This special process creates the unique ecological GreenLINE Floor
1. Grinding
2. Refining
3. Polishing
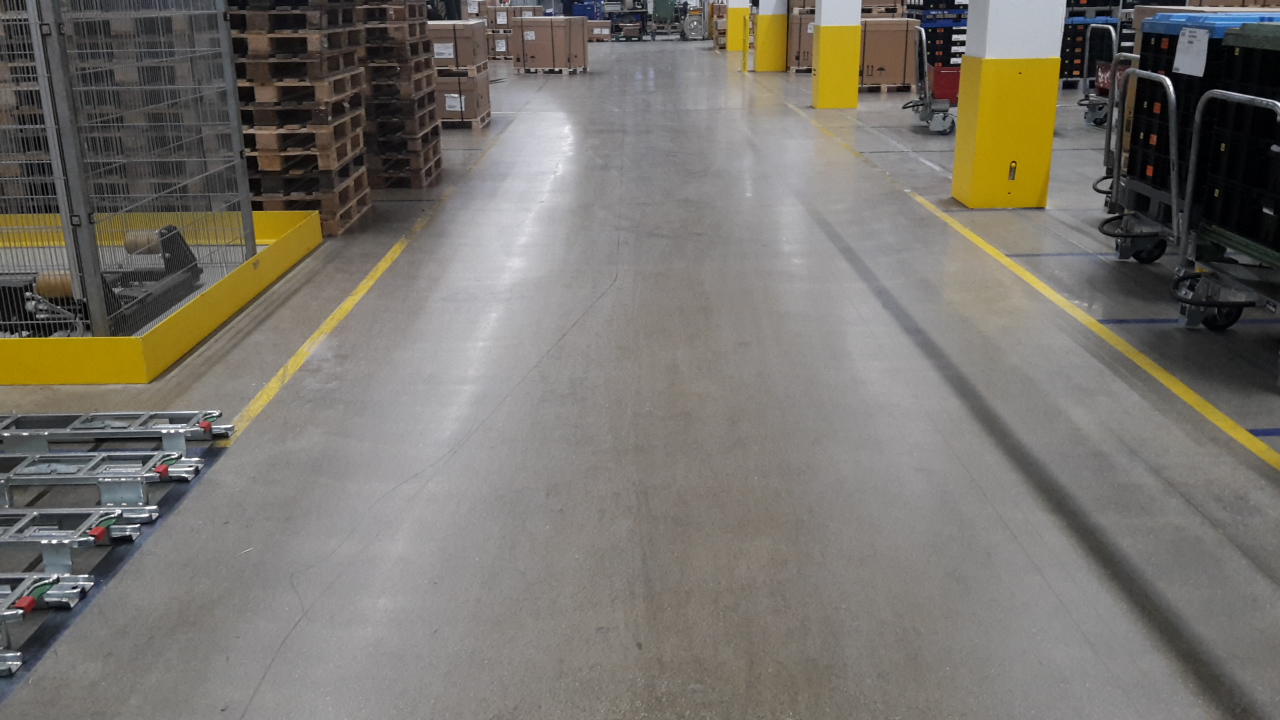
One procedure – many advantages
Functional and cost-effective construction and Refurbishment:
Sustainable and value retention:
Safety and additional value:
Often accidents are caused by soiling and slickness which frequently can lead to production interruptions
Examples of use:
- Production halls
- Logistic centres
- Warehouses
- Public buildings such as schools, museums, airports, railway stations etc.
- Retail stores
Technical Properties of GreenLine Floor
Look:
Anti-slip class (class R):
Ingredients:
Impregnations:
Flammability:
Life span:
Resistance:
- Oils
- Lye
- Acids
Cleaning:
Awards:
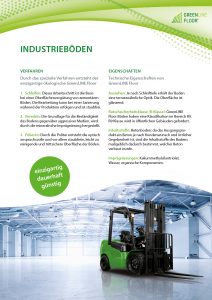
Do you have any questions?
Clara-Schumann-Weg 29
D- 73770 Denkendorf
Phone: 0711 – 94 58 71 60
*Mandatory field. Detailed information on how we handle user data can be found in our Privacy Policy.